别划走!这些都是染色疵病分析,有图有真相!收藏必备~
- 分类:快讯
- 编辑:针织工业
- 来源:针织工业
- 日期:2020-12-02 09:41
染色制品所得色泽深浅不一,色光有差异。根据色差的不同又分为同批色差和同匹色差。同批色差是指在同批产品中,一个色号的产品,箱与箱之间、件与件之间、包与包之间、匹与匹之间存在色差。同匹色差是指同匹产品中的边中色差、前后色差或正反面等位置上的色差

染色制品所得色泽深浅不一,色光有差异。根据色差的不同又分为同批色差和同匹色差。同批色差是指在同批产品中,一个色号的产品,箱与箱之间、件与件之间、包与包之间、匹与匹之间存在色差。同匹色差是指同匹产品中的边中色差、前后色差或正反面等位置上的色差。
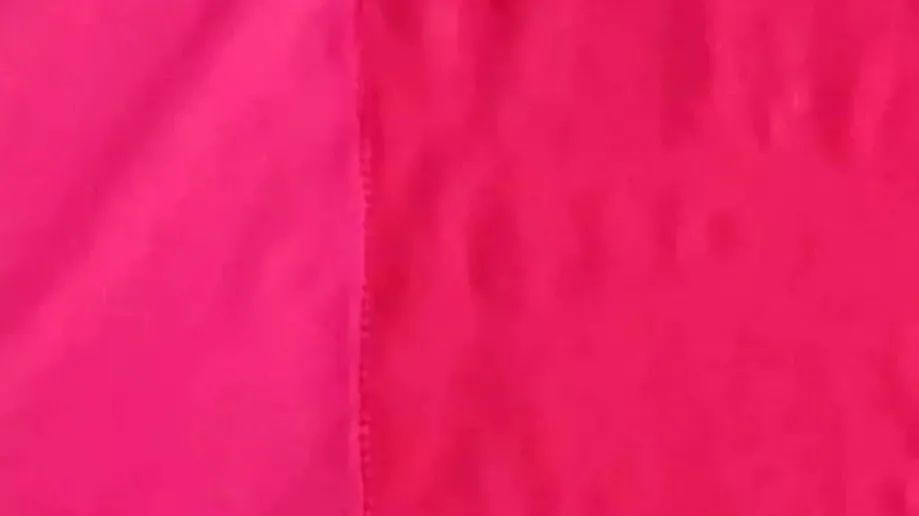
加强坯检,保证坯布质量 选用合适设备、采用均匀轧车或改善轧车的均匀性 加强练漂管理,提供合格半制品 同一批染物采用相同坯布 染前布面干燥要均匀一致 染前定型效果要均匀 丝光后布面pH值控制中性 合理选择染料(上染曲线相似、加强染料测试等) 染色时加入匀染性助剂 染色工艺合理 重视染后处理,水洗、皂洗要充分 后整理助剂选择要慎重,工艺条件要一致
染色成品的色泽与指定的样品色泽不符,并超过了允许色差标准。 
表现为: 不符同类布样(生产实样与原样属相同纤维、相同组织的色样) 不符参考样(不同原料不同组织的色泽) 不符成交小样(提供给客户并经双方确定的样品) 不符数字样(客户提供的电脑测配色系统的数字样)
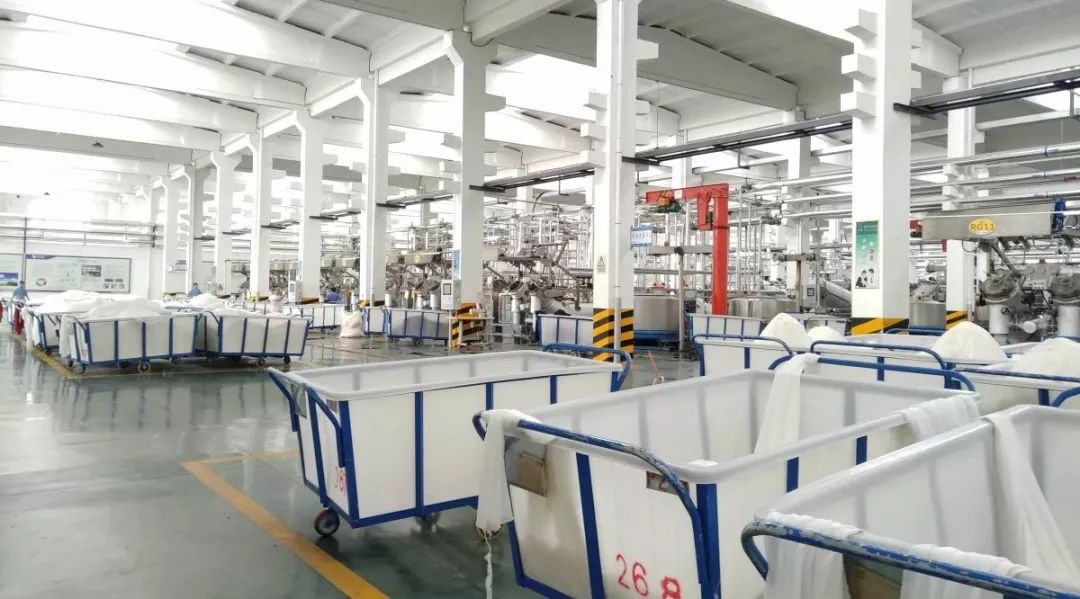
染色工艺制定不当,大小样生产条件不相同
审核色样光源不统一 染色计划安排不周 染料、助剂分批管理不善 染色工艺条件、操作掌握不好 半制品不符要求 染色采用硬水 染色管理不妥 染化料量称错 染色中没有严格掌握工艺条件
加强坯布检验。 根据纤维性质,选用匀染性好的染料。 加强前处理,确保半制品质量。 轧余率要均匀; 加入匀染性助剂; 采用的染料达到要求的细度范围; 烘干时温度由低到高,避免染料产生泳移。 染色工艺合理,并严格控制工艺条件。 加强设备检查、调试。
色渍深于布面颜色的斑渍。最常见出现在使用分散艳蓝,分散翠兰,分散红玉等染料的色系上,由于染料的特殊性染料自身原因,染料没化开,升温快慢等直接导致色渍产生。
染料的聚集:染料聚集体沉积在织物上而造成(包括增白剂聚集体沉积)
加强织物前处理 严防染料凝聚 选用凝聚性较小的染料 选用性能优良的匀染剂或分散剂 避免和减少色淀产生(化料规范、加扩散剂)
色 点
在染色织物上无规律地呈现出色泽较深的细小点。(包括白点)
色点产生的原因也很多,如白点,可能是非成熟棉不上染染料的原因,也可能是纯碱、元明粉等固体沾在布上造成局部不上染等原因。
|